Application of ferrosilicon inoculants: At present, camshafts of gasoline and diesel engines are generally made of steel, alloy cast iron, and ductile iron, and use quenching or cold shock processes (alloy cast iron process) to meet comprehensive performance requirements. However, steel shafts and ductile iron shafts are not suitable for high-speed engines greater than 4000 rpm, and the strength of cold-shock alloy cast iron is not suitable for the strength requirements of medium-sized engines.
The function of the ferrosilicon inoculant is to overcome the existing technology's steel or ductile iron material is not suitable for the anti-wear requirements of high-speed engines and the cold-shock alloy cast iron material is not suitable for the material strength requirements of medium and low-speed engines, and provides a method suitable for all types of engines. A cold-shock alloy ductile iron and camshaft casting method that meets the requirements for engine wear resistance, scratch resistance, spalling resistance, fatigue point contact mechanical strength, etc. The use of ferrosilicon inoculant conforms to the trend of engine development towards low consumption and energy saving. The ferrosilicon inoculant adopts a random large-dose inoculation method, and the total silicon content is 1.9%-3.7%. Pre-furnace testing shows the carbon equivalent of the original hot metal, the carbon equivalent of the nodularizing agent (actual inspection of the burning amount) and the carbon equivalent of the ferrosilicon inoculant ( The total amount of absorption is between 4.3-4.55. It is smelted in a power frequency or intermediate frequency furnace, and the furnace temperature is 1450°C. The camshaft casting method of cold-shock alloy ductile iron is green sand molding, wet casting, and the molding sand moisture is less than 4%; the pouring temperature is 1340-1360°C; the thickness of the external cooling iron is 0.25-0.4 of the outer diameter of the cam peach, and the width of the external cooling iron The same width as the cam peach. The length of the outer cooling iron is the radial size of the cam peach after parting + 2 times the thickness of the cold iron. The inner cavity of the outer cooling iron is the actual radial size of the side of the cam peach box + 2mm on one side. The periphery can be Any shape, with a slope of 1-2° from bottom to top.
AnYang zhaojin ferroalloy co.,Ltd
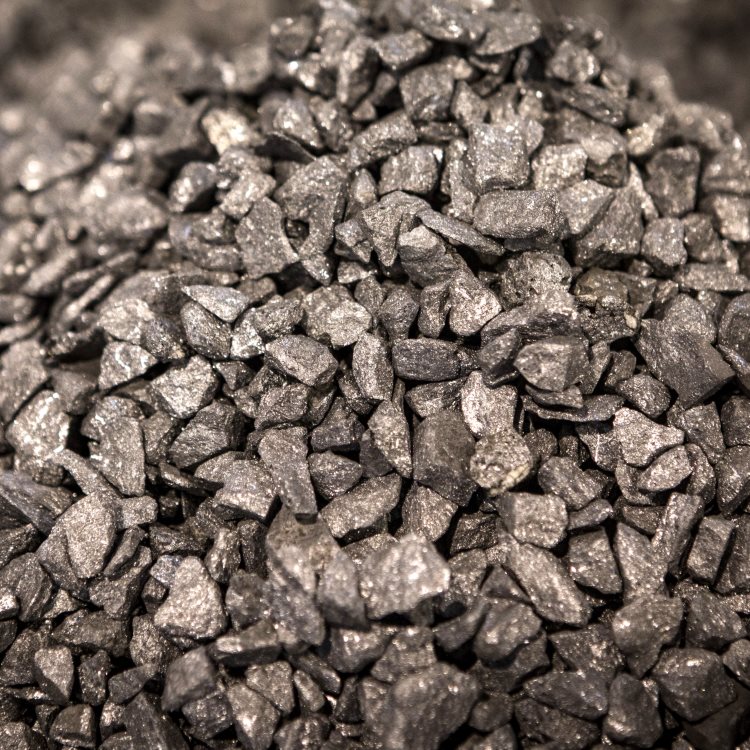
Post time: Nov-03-2023